The relentless pursuit of computational power in the realm of digital asset generation inherently produces a formidable byproduct: heat. For anyone involved in the demanding world of cryptocurrency mining, understanding and mastering the principles of thermal management is not merely an operational nicety; it is an absolute imperative for long-term viability, profitability, and hardware longevity. The sustained operation of high-performance mining equipment, whether it be Application-Specific Integrated Circuits (ASICs) or Graphics Processing Units (GPUs), pushes components to their thermal limits. Without meticulous temperature regulation, these powerful machines can suffer from reduced efficiency, premature wear, and catastrophic failure, turning potential profits into significant losses.
The physics behind heat generation in mining hardware is straightforward: electrical energy, consumed to perform complex cryptographic computations, is not entirely converted into useful work. A substantial portion is dissipated as thermal energy due to electrical resistance within circuits, inefficiencies in power conversion, and the rapid switching of transistors. This heat, if not effectively removed, accumulates, leading to elevated component temperatures. Modern semiconductor devices are designed to operate within specific thermal envelopes, typically ranging from 0°C to 95°C for core components. Exceeding these limits, even intermittently, can trigger thermal throttling – a mechanism where the hardware automatically reduces its clock speed and voltage to lower heat output. While throttling protects the hardware from immediate damage, it directly translates to a significant drop in computational power, diminishing mining output and, consequently, revenue. More critically, prolonged exposure to elevated temperatures accelerates the degradation of semiconductor junctions, capacitors, and solder joints, drastically shortening the operational lifespan of expensive mining equipment. Studies have consistently demonstrated that for every 10°C increase above an optimal baseline, the expected lifespan of typical silicon components can be halved. Imagine the financial impact of replacing a fleet of high-end ASIC miners, each costing several thousand dollars, a year or two before their expected end-of-life due to preventable thermal stress. This underscores the critical importance of a robust, proactive thermal management strategy.
Understanding the ambient conditions in which your mining hardware operates is the foundational step in any effective cooling strategy. Environmental factors exert a profound influence on the efficiency and reliability of cooling systems, often dictating the scope and complexity of the solutions required. The air temperature surrounding your equipment is perhaps the most obvious variable. If the intake air is already warm, the cooling system has less capacity to dissipate the heat generated by the hardware. For instance, a mining operation in a tropical climate with average ambient temperatures of 30-35°C (86-95°F) will face significantly greater cooling challenges than one situated in a Nordic country where temperatures may average 5-10°C (41-50°F). The effectiveness of conventional air cooling, which relies on a temperature differential to transfer heat, diminishes rapidly as ambient temperatures rise. This necessitates more powerful fans, larger radiators, or a transition to more advanced cooling methodologies.
Humidity, often overlooked, is another critical environmental factor. High humidity levels, especially when combined with lower temperatures, can lead to condensation on hardware components, which is a direct pathway to short circuits and corrosion. While condensation is less common in hot, high-humidity mining environments due to the higher operating temperatures of the hardware preventing the components from dropping below the dew point, it remains a risk, particularly during system shutdowns or in environments with rapid temperature fluctuations. Conversely, extremely low humidity can increase the risk of static electricity discharge, which can damage sensitive electronics. Maintaining relative humidity levels between 40% and 60% is generally considered optimal for electronic equipment. Specialized dehumidifiers or humidifiers might be necessary in extreme environments to maintain this balance.
Air quality, specifically the presence of dust and particulate matter, poses a continuous threat to air-cooled mining systems. Dust acts as an insulating layer, accumulating on heatsinks, fan blades, and component surfaces. This buildup impedes heat transfer, reducing the efficiency of cooling fins and restricting airflow. Over time, a thick layer of dust can effectively choke a cooling system, leading to dramatically higher operating temperatures. Regular cleaning protocols are indispensable to combat this. Furthermore, corrosive airborne contaminants, such as sulfur compounds often found in industrial areas, can accelerate the degradation of metallic components and solder joints, necessitating advanced air filtration or sealed environments.
Altitude also plays a subtle but noticeable role. At higher altitudes, air density decreases, meaning there are fewer air molecules to transfer heat away from components. While this effect might be negligible for small-scale operations, large data centers or mining farms situated at significant elevations (e.g., above 1,500 meters or 5,000 feet) might experience a minor reduction in air cooling efficiency, requiring slightly more aggressive airflow or lower ambient temperature targets.
Finally, the proximity to other heat-generating equipment or external heat sources can inadvertently raise the effective ambient temperature for your mining hardware. Poorly ventilated rooms, insufficient spacing between rigs, or even sunlight striking equipment directly can create localized hot spots that undermine even well-designed cooling strategies. A comprehensive understanding of these environmental variables forms the bedrock for selecting and implementing the most appropriate and effective thermal management solutions for your specific mining operation.
Fundamental Principles of Heat Transfer in Cooling Systems
To effectively manage thermal loads, it’s crucial to grasp the basic mechanisms by which heat moves. These principles form the foundation of all cooling technologies employed in mining.
Conduction: This is the transfer of heat through direct physical contact between objects or within a single object. In mining hardware, heat is conducted from the silicon chip (die) through the integrated heat spreader (IHS) or thermal pads/paste to the heatsink. The efficiency of conduction depends on the thermal conductivity of the materials involved. Materials like copper and aluminum are excellent thermal conductors, which is why they are predominantly used in heatsinks and heat pipes. Thermal interface materials (TIMs) like thermal paste or thermal pads are applied between the hot component and the heatsink to fill microscopic air gaps, which are poor conductors of heat, thereby maximizing heat transfer through conduction.
Convection: This is the transfer of heat through the movement of fluids (liquids or gases). In air-cooled systems, fans create airflow, moving cooler ambient air over the hot heatsink fins. The air absorbs heat from the fins and then carries that heat away, exhausting it from the system. This is known as forced convection. Natural convection also occurs, where warmer, less dense air rises and cooler, denser air sinks, but it is far less effective for high-density heat sources like mining hardware. Liquid cooling systems utilize forced convection by circulating a coolant over hot components, transferring heat to the liquid, which then carries the heat to a radiator where it can be dissipated.
Radiation: This is the transfer of heat through electromagnetic waves, requiring no medium. All objects above absolute zero emit thermal radiation. While heatsinks do radiate some heat, this mechanism is generally a minor contributor to the overall cooling of mining hardware compared to conduction and convection, especially in environments with active airflow. Its contribution becomes more significant in passive cooling scenarios or very high-temperature applications. The surface area and emissivity of a material influence its radiative heat transfer. Dark, matte surfaces tend to radiate heat more effectively than shiny, polished ones.
An effective cooling system will leverage these principles in concert. For instance, a GPU cooler conducts heat from the GPU die to its heatsink fins (conduction), and then fans blow air over these fins to carry the heat away (convection). In a liquid-cooled system, heat conducts from the chip to the water block, then convects into the fluid, which then convects the heat to a radiator, where it is transferred to the air (convection) and then exhausted. Understanding these fundamentals allows for informed decisions regarding cooling hardware selection and system design.
Air Cooling Strategies: The Workhorse of Mining Thermal Management
Air cooling remains the most prevalent and accessible method for thermal management in mining operations, ranging from single-rig setups to multi-megawatt farms. Its simplicity, relatively low cost, and ease of deployment make it a popular choice. However, maximizing its effectiveness requires more than simply pointing a fan at your hardware.
Fan Selection and Configuration
The choice and arrangement of fans are paramount. Not all fans are created equal, and their performance is measured by several key metrics:
- Cubic Feet per Minute (CFM): This indicates the volume of air a fan can move per minute. Higher CFM generally translates to better cooling, but often at the cost of increased noise and power consumption.
- Static Pressure: This refers to a fan’s ability to push air through restrictive environments, such as dense heatsink fins or dust filters. Fans designed for high static pressure are crucial for effective cooling within enclosed cases or through tightly packed radiators.
- Noise Level (dBA): An important consideration, especially for residential setups. High-performance server fans, while moving vast amounts of air, can generate noise levels comparable to jet engines, making them unsuitable for home use.
- Power Consumption: Enterprise-grade fans, while powerful, can consume significant wattage, adding to the overall operational expenditure.
For GPU mining rigs, a common strategy involves using multiple high-airflow case fans to create a strong unidirectional flow of air through the rig. For ASICs, which typically come with integrated, powerful centrifugal or axial fans, the focus shifts to ensuring these fans have an unimpeding path for intake and exhaust.
Airflow Dynamics: Positive vs. Negative Pressure
Controlling the internal air pressure within a mining enclosure or room can significantly impact cooling efficiency and dust accumulation.
- Positive Pressure: Achieved when the total CFM of intake fans exceeds the total CFM of exhaust fans. This creates a slightly higher internal pressure, forcing air out of all available gaps and preventing unfiltered air (and dust) from being drawn in. It’s excellent for keeping dust out but requires good filtration on intake fans.
- Negative Pressure: Achieved when the total CFM of exhaust fans exceeds the total CFM of intake fans. This draws air in through all available openings. While it can be effective for quickly expelling hot air, it also pulls in unfiltered air and dust, necessitating more frequent cleaning.
- Balanced Pressure: Aiming for equal intake and exhaust CFM. This is often the ideal, balancing effective cooling with dust control, assuming good filtration on intake.
For open-air GPU rigs, the concept applies to the room itself. Ensuring a dedicated cool air intake and hot air exhaust path for the entire mining space is crucial. For example, a common error is exhausting hot air into an attic space without proper ventilation, leading to recirculation of hot air back into the mining area.
Hot Aisle/Cold Aisle Containment
For larger-scale mining operations or those utilizing rack-mounted ASICs, the hot aisle/cold aisle containment strategy, borrowed from data center design, is highly effective. This involves arranging racks in rows, creating alternating aisles for cool air intake (cold aisles) and hot air exhaust (hot aisles).
- Cold Aisles: Supply cool air directly to the front (intake) of the mining hardware.
- Hot Aisles: Collect hot exhaust air from the rear of the mining hardware.
Containment systems, such as curtains or panels, are then used to physically separate these aisles, preventing the mixing of hot and cold air. This ensures that the hardware always receives the coldest possible intake air, maximizing cooling efficiency and reducing the workload on cooling units. Implementing hot/cold aisle containment can result in a 15-20% improvement in cooling efficiency compared to unmanaged airflow in a large setup, translating directly to lower power consumption for cooling or higher hardware densities.
Dust Filtration and Maintenance
As previously mentioned, dust is the nemesis of air-cooled systems. Implementing effective dust filtration on all air intake points is crucial. Regularly cleaning or replacing these filters is a non-negotiable maintenance task. Neglecting filters not only reduces airflow but also traps dust, which can then be ingested by the fans, leading to premature bearing wear and reduced lifespan. For example, a typical 100-micron filter should be cleaned monthly in a dusty environment, or more frequently if visual inspection reveals significant buildup. Failure to do so can lead to a 5°C to 10°C increase in GPU core temperatures within a few weeks due to restricted airflow and insulating dust layers on heatsinks.
Strategic Rig Placement
Even in smaller operations, thoughtful placement of mining rigs can yield significant thermal benefits. Avoid placing rigs directly against walls or in corners where airflow can become stagnant. Ensure adequate spacing between rigs to allow for proper air circulation. Consider the natural convection of heat – hot air rises. Positioning exhaust fans at higher points in a room and intake fans lower can assist in creating natural airflow patterns that complement forced convection. For instance, elevating rigs off the floor on open racks improves airflow underneath and around the units, preventing heat traps.
Liquid Cooling Solutions: Beyond Air for Extreme Performance
When air cooling reaches its limits – either due to extreme heat generation, ambient temperature constraints, or the desire for greater power efficiency and hardware longevity – liquid cooling emerges as a powerful alternative. Liquid has a significantly higher specific heat capacity and thermal conductivity than air, meaning it can absorb and transfer far more heat per unit volume.
All-in-One (AIO) Liquid Coolers for GPUs
AIO coolers, common in enthusiast PC builds, are pre-filled, closed-loop liquid cooling systems that offer a relatively simple entry into liquid cooling. They typically consist of a pump integrated with a cold plate that mounts directly onto the GPU, connected by tubing to a radiator and fan assembly.
Pros:
- Better Performance: Significantly better thermal dissipation than stock air coolers, often reducing GPU core temperatures by 15-25°C. This allows for higher stable clock speeds and improved hash rates.
- Reduced Noise: AIOs often allow for lower fan speeds on the radiator compared to the loud, high RPM fans on stock air coolers, leading to quieter operation.
- Easier Installation: Compared to custom loops, AIOs are much simpler to install, requiring no complex tubing or fluid management.
Cons:
- Cost: More expensive than traditional air coolers.
- VRAM Cooling: While excellent for the GPU core, many AIOs do not directly cool the VRAM modules or VRMs, which can still overheat on demanding mining algorithms (e.g., Ethereum before The Merge, Kaspa now). Supplemental cooling for these components (e.g., small heatsinks with fans) may be necessary.
- Pump Failure: Like any mechanical component, the pump is a potential point of failure.
Custom Loop Liquid Cooling
For the most demanding GPU mining rigs or specialized setups, custom liquid cooling loops offer unparalleled performance and flexibility. These systems involve individual components: a pump, reservoir, CPU/GPU water blocks, tubing, fittings, and radiators.
Pros:
- Superior Cooling: By far the most effective method for dissipating heat from multiple components (GPU core, VRAM, VRMs, CPU). Allows for extreme overclocking and sustained high performance.
- Customization: Highly customizable in terms of aesthetics, component choice, and layout.
- Lower Noise: A well-designed custom loop with large radiators can dissipate heat silently or with very low fan speeds.
Cons:
- Complexity & Cost: Significant upfront investment and complex installation, requiring careful planning and leak testing.
- Maintenance: Requires periodic fluid replacement (e.g., annually) and cleaning of components.
- Leak Risk: Though rare with proper installation, a leak can cause catastrophic damage to hardware.
Custom loops are particularly advantageous for GPU mining rigs using multiple high-power GPUs. By using full-cover water blocks that cool both the GPU die and the surrounding memory and VRM components, these systems can maintain the entire card at optimal temperatures, pushing performance boundaries safely. For example, a rig with eight RTX 3080 GPUs, notorious for their hot GDDR6X memory, can see VRAM junction temperatures drop from 100-105°C (throttling range) to a stable 70-80°C with custom water blocks, significantly extending their lifespan and maintaining maximum hash rates.
Immersion Cooling: The Future of High-Density Mining
Immersion cooling represents the pinnacle of thermal management for mining, especially for high-density ASIC farms or large GPU deployments. This technique involves submerging hardware directly into a non-conductive dielectric fluid.
Types of Immersion Cooling:
- Single-Phase Immersion Cooling: Hardware is submerged in a liquid (e.g., mineral oil, synthetic dielectric fluids) that remains in its liquid phase. The heated fluid is then pumped through a heat exchanger (radiator) to dissipate heat to the air or a secondary water loop.
Pros:
- Exceptional Cooling: Far superior to air or even conventional liquid cooling. Fluids are in direct contact with every component, providing uniform and highly efficient heat transfer.
- Noise Reduction: Fans are eliminated from the submerged hardware, dramatically reducing operational noise.
- Dust/Corrosion Protection: Hardware is sealed from the environment, protecting against dust, humidity, and corrosive elements.
- Increased Hardware Lifespan: Stable, lower temperatures and protection from environmental factors can significantly extend hardware longevity.
- Higher Density: Allows for packing more hardware into a smaller footprint due to superior heat dissipation.
Cons:
- High Initial Cost: Significant upfront investment in tanks, fluids, pumps, and heat exchangers.
- Messy Maintenance: Working with submerged hardware can be messy.
- Fluid Degradation: Fluids can degrade over time, requiring periodic replacement or filtration.
- Component Compatibility: Certain materials (e.g., some plastics, glues) may react negatively with specific dielectric fluids, requiring careful selection of hardware or fluid.
- Two-Phase Immersion Cooling: A more advanced and efficient method where the hardware is submerged in a dielectric fluid with a very low boiling point. As the hardware heats up, the fluid boils, turning into vapor. This vapor rises, condenses on a cooled surface (condenser coil) within the tank, and then drips back down as liquid, creating a continuous heat transfer cycle.
Pros:
- Even Greater Efficiency: Leveraging the latent heat of vaporization makes it incredibly efficient at transferring large amounts of heat.
- No Pumps Needed for Circulation: The phase change drives circulation, reducing mechanical complexity (though external cooling for the condenser is still required).
- Extremely Low Operating Temperatures: Hardware can run remarkably cool, extending lifespan and maximizing performance.
Cons:
- Exorbitant Cost: The dielectric fluids used are extremely expensive (often per gallon), making the initial investment very high.
- Fluid Containment: Requires specialized sealed tanks to prevent vapor escape.
- Limited Fluid Options: Fewer compatible fluids are available compared to single-phase.
Immersion cooling is particularly well-suited for large-scale ASIC farms where heat density is immense. A 10 MW ASIC farm could potentially reduce its cooling power consumption by 30-50% by switching from air to single-phase immersion cooling, leading to millions of dollars in annual energy savings. Furthermore, the waste heat from immersion cooling can be more readily captured for secondary uses, such as heating buildings or greenhouses, unlocking additional economic value from the mining process.
Monitoring and Control: The Eyes and Brain of Your Thermal Strategy
Effective temperature management is not a set-it-and-forget-it endeavor. It requires continuous monitoring, intelligent data analysis, and responsive control mechanisms. Without these elements, even the most robust cooling infrastructure can fail to deliver optimal results.
Software-Based Monitoring Tools
For individual rigs and smaller operations, various software utilities provide granular insights into hardware temperatures.
- Hardware Monitoring Software (e.g., HWMonitor, HWiNFO64): These tools provide real-time readings for CPU core temperatures, GPU core temperatures, VRAM temperatures (junction temperature for GDDR6/6X), VRM temperatures, and fan speeds. They are essential for initial setup and troubleshooting.
- Mining Operating Systems (e.g., HiveOS, RaveOS): Dedicated mining operating systems offer integrated monitoring dashboards that display temperatures, fan speeds, power consumption, and hash rates for all GPUs or ASICs in a farm. They typically allow for remote monitoring and basic fan curve adjustments.
- Manufacturer-Specific Software (e.g., MSI Afterburner, Gigabyte Aorus Engine): These utilities, designed for graphics cards, offer advanced controls for fan curves, voltage, and clock speeds, allowing miners to fine-tune the thermal performance of their GPUs.
- Custom Scripts and APIs: For larger operations, custom scripts (e.g., Python, PowerShell) interacting with hardware APIs or OS-level sensor data can provide highly customized monitoring, logging, and alert capabilities, integrating with existing network monitoring solutions.
Sensor Types and Placement
Understanding the different temperature points within your hardware is crucial for comprehensive monitoring:
- Core Temperature: The temperature of the main processing die (CPU or GPU). This is typically the most commonly reported temperature.
- Junction Temperature (TJunction): For modern GDDR6/GDDR6X memory modules, this is the hottest point on the memory die. This reading is critical for stability and longevity, as these memory types are highly susceptible to thermal throttling and degradation above certain thresholds (often 95-105°C). Ensuring VRAM junction temperatures are below 90°C is a common goal for optimal operation.
- Hotspot Temperature: On some GPUs, this indicates the hottest point on the entire GPU package, which can sometimes be significantly higher than the reported core temperature.
- VRM (Voltage Regulator Module) Temperature: These components deliver power to the GPU and memory and can generate substantial heat. Monitoring VRM temperatures is important, as overheating can lead to instability or component failure.
Strategically placed external temperature sensors can provide invaluable data about ambient conditions within the mining space, helping to identify hot spots or confirm the efficacy of air circulation. These might include thermistors or thermocouples positioned near air intake/exhaust points, between rigs, or at different elevations.
Setting Thresholds and Alerts
Passive monitoring is insufficient. Proactive temperature management requires setting intelligent thresholds and configuring alerts.
- Warning Thresholds: Set slightly below critical temperatures (e.g., 80-85°C for GPU cores, 90-95°C for VRAM junction). When temperatures hit these levels, an alert (email, SMS, notification to a dashboard) should be triggered, prompting manual intervention.
- Critical Thresholds & Automated Actions: Set at the absolute maximum safe operating temperature (e.g., 90°C for GPU cores, 100°C for VRAM junction). If temperatures reach these points, automated actions should be triggered, such as:
- Increasing fan speeds to maximum.
- Reducing power limits or core clock speeds (if not already throttled).
- Initiating a graceful shutdown of the affected hardware to prevent damage.
These automated responses are invaluable, particularly for remote operations or during off-hours, preventing costly downtime and hardware damage. Implementing custom fan curves that dynamically adjust fan speeds based on temperature readings is a common and effective control mechanism, allowing fans to spin faster only when needed, reducing noise and power consumption during cooler periods.
Remote Monitoring and Management Systems
For any serious mining operation, whether a multi-rig home setup or a large farm, remote monitoring and management are indispensable. Cloud-based platforms or local network monitoring systems allow operators to check temperatures, adjust settings, and respond to alerts from anywhere with an internet connection. This capability is crucial for minimizing downtime and ensuring continuous optimal performance without constant physical presence. Integrating environmental sensors (ambient temperature, humidity) with hardware monitoring provides a holistic view of the thermal environment, enabling operators to correlate external conditions with hardware performance and anticipate issues.
Preventative Maintenance: The Backbone of Longevity
Even the most sophisticated cooling systems will falter without consistent preventative maintenance. Proactive care ensures sustained efficiency, prevents unexpected failures, and significantly extends the operational lifespan of your mining hardware. This often overlooked aspect is critical for long-term profitability.
Regular Cleaning Routines
Dust and debris are the primary enemies of air-cooled systems. Over time, they accumulate on heatsinks, fan blades, and ventilation grilles, acting as an insulating layer that traps heat and impedes airflow.
- Frequency: The cleaning schedule depends heavily on the operating environment. In a relatively clean residential setting, a thorough cleaning every 3-6 months might suffice. In a dusty industrial setting, or if using negative pressure systems without robust filtration, monthly or even bi-weekly cleaning might be necessary.
- Method:
- Compressed Air: Use short bursts from a can of compressed air or a low-pressure air compressor (with a moisture trap) to dislodge dust from heatsinks, fans, and circuit boards. Ensure fans are held stationary to prevent overspinning and damage to bearings.
- Soft Brushes & Microfiber Cloths: Gently brush away stubborn dust from sensitive components and wipe down surfaces.
- Vacuum Cleaners: Use a low-power vacuum with a brush attachment for larger dust clumps, but avoid direct contact with circuit boards to prevent static discharge.
- Filter Maintenance: If using air filters on intake fans or room ventilation, regularly clean or replace them. Clogged filters dramatically reduce airflow. A visual inspection should be part of the weekly routine, with cleaning/replacement as needed.
Thermal Interface Material (TIM) Replacement
The thermal paste or pads between the GPU/CPU die and its heatsink are critical for efficient heat transfer. Over time, thermal paste can dry out, crack, or pump out, losing its effectiveness. Thermal pads can compress, degrade, or become brittle.
- Frequency: While thermal paste on CPUs can last for years in a typical PC, the sustained high temperatures and vibrations in mining rigs can accelerate its degradation. For mining GPUs, particularly those with hot GDDR6X memory, replacing thermal pads and paste every 12-18 months (or sooner if junction temperatures are consistently high despite adequate airflow) can lead to significant temperature drops (e.g., 10-20°C decrease in VRAM junction temps). For ASICs, replacement intervals are typically longer, often aligned with major maintenance cycles, but should be considered if specific chips are running hotter than others in the batch.
- Process:
- Disassemble the cooler from the GPU/CPU.
- Carefully clean off old thermal paste with isopropyl alcohol and a lint-free cloth. For thermal pads, remove old ones and clean the surfaces thoroughly.
- Apply new, high-quality thermal paste (e.g., Arctic MX-4, Noctua NT-H1) in a pea-sized dot or line.
- For VRAM, apply new thermal pads of the correct thickness and thermal conductivity (e.g., Gelid GP-Extreme, Thermalright Odyssey). Incorrect pad thickness can prevent proper contact or over-compress, causing issues.
- Reassemble the cooler, ensuring even pressure.
Fan Health and Replacement
Fans are mechanical components with finite lifespans. Bearing wear can lead to increased noise, reduced RPM, and eventual failure.
- Monitoring: Regularly monitor fan RPMs through software. A significant drop in RPM for a given temperature, or an increase in unusual noise (grinding, whining), indicates impending fan failure.
- Replacement: Have spare fans on hand, especially for critical positions or hard-to-source models (common for ASIC fans). Proactively replace fans showing signs of wear before they fail completely, preventing overheating and downtime. For large farms, a preventative replacement schedule (e.g., every 2-3 years for heavy-duty server fans) can be more cost-effective than reactive replacement.
Liquid Coolant Maintenance (for Custom Loops & Immersion)
Liquid cooling systems, while efficient, require their own set of maintenance protocols.
- Custom Loops:
- Fluid Replacement: Coolant (distilled water with biocide/corrosion inhibitors, or specialized pre-mixes) should be replaced annually, or more frequently if it discolors or shows signs of algae growth.
- Component Cleaning: Radiators, water blocks, and reservoirs should be periodically flushed and cleaned to remove any particulate buildup or residue.
- Leak Inspection: Regularly inspect tubing, fittings, and connections for any signs of leaks or degradation.
- Immersion Systems:
- Fluid Filtration/Analysis: Dielectric fluids can degrade or accumulate particulates over time. Regular fluid analysis can determine when filtration or replacement is necessary. Larger systems might incorporate continuous filtration.
- Tank Cleaning: Periodically empty and clean immersion tanks to remove any sediment or debris.
- Hardware Inspection: When hardware is removed for maintenance or upgrades, inspect it for any fluid-related issues or material degradation.
Firmware and Software Updates
Manufacturers occasionally release firmware updates for GPUs, ASICs, or motherboard BIOS that can include optimized fan curves, power efficiency improvements, or bug fixes that indirectly impact thermal performance. Staying up-to-date can contribute to more stable and cooler operation. Similarly, updates to mining software or operating systems can sometimes offer better thermal management algorithms.
By integrating these preventative maintenance tasks into a regular schedule, miners can significantly enhance the reliability and lifespan of their hardware, transforming what might seem like an operational overhead into a strategic investment that yields consistent returns and minimizes costly disruptions.
Optimizing for Specific Hardware: GPUs vs. ASICs
While the fundamental principles of thermal management apply universally, the specific needs and optimal strategies vary significantly between GPU mining rigs and ASIC miners due to their design, scale, and heat output characteristics.
Graphics Processing Units (GPUs)
GPU mining, particularly with high-end cards from NVIDIA (RTX series) and AMD (RX series, RDNA architecture), presents unique thermal challenges. Modern GPUs are designed for bursty workloads in gaming, but continuous, 24/7 cryptographic hashing places sustained, intense thermal load on specific components.
Key Thermal Concerns for GPUs:
- GPU Core Temperature: This is the most commonly reported temperature. Aim for 60-70°C for optimal performance and longevity. Most GPUs will start throttling around 80-85°C.
- VRAM Junction Temperature: For GDDR6 and especially GDDR6X memory (found on NVIDIA RTX 3070 Ti, 3080, 3080 Ti, 3090, 3090 Ti, 4070 Ti SUPER, 4080 SUPER, 4090), this is often the most critical temperature. GDDR6X is particularly sensitive, with throttling often beginning at 95-100°C and a theoretical maximum operating temperature of 105-110°C. Sustained operation above 90-95°C can accelerate memory degradation. Reducing this temperature is paramount for stability and longevity.
- VRM Temperature: Voltage Regulator Modules convert the incoming power supply voltage to the specific voltages required by the GPU core and memory. They can become very hot under sustained load. While often less critical than core or VRAM temps, excessively high VRM temperatures (e.g., above 110-120°C for some designs) can lead to instability and component failure.
GPU Specific Thermal Strategies:
- Open-Air Rig Frames: Unlike enclosed PC cases, open-air frames promote natural convection and allow for better airflow management around multiple GPUs. This design prevents hot air from recirculating between cards.
- Strategic Fan Placement: For open rigs, use high-CFM axial fans (e.g., 120mm or 140mm server fans or larger industrial fans) positioned to create a clear intake-to-exhaust path across the entire row of GPUs. For example, intake fans at one end of the rig pushing air over the GPUs, and exhaust fans at the other end pulling hot air away.
- Under-volting and Power Limiting: Reducing the GPU’s core voltage and power limit (through software like MSI Afterburner or mining OS settings) is one of the most effective ways to lower temperatures without significant hash rate loss. Often, a 10-20% reduction in power draw can lead to a disproportionate decrease in heat output (e.g., 5-10°C temperature drop) while only reducing hash rate by 1-5%. This greatly improves efficiency (hash rate per watt) and thermal performance.
- Thermal Pad and Paste Replacement: As detailed in the maintenance section, this is particularly impactful for GDDR6X cards. Replacing stock thermal pads with high-quality aftermarket pads (e.g., Gelid GP-Extreme, Thermalright Odyssey) of the correct thickness can drop VRAM junction temperatures by 15-30°C on hot cards like the RTX 3080/3090. This single upgrade can transform an unstable, throttling card into a cool, high-performing miner.
- Backplate Cooling: Many modern GPUs have metal backplates that can get very hot due to heat transfer from the PCB and VRAM modules on the back of the card. Attaching small heatsinks and/or fans to the backplate can provide additional passive or active cooling, especially for the VRAM modules that are often located on the back of the PCB.
- AIO or Custom Liquid Cooling: For individual high-power GPUs or densely packed rigs, transitioning to AIO or custom liquid cooling is the ultimate solution for maintaining low core, VRAM, and VRM temperatures, allowing for maximum stable clock speeds and extended lifespan.
Application-Specific Integrated Circuits (ASICs)
ASICs are purpose-built for a single cryptographic algorithm, allowing for extreme efficiency and hash rate density. However, this specialization also means they generate immense heat in a compact footprint. Unlike GPUs, ASICs generally have less user-serviceable thermal components; their cooling systems are typically integrated and factory-designed for high performance.
Key Thermal Concerns for ASICs:
- Chip Temperature (Hash Board Temperature): ASICs contain numerous hash boards, each populated with hundreds of specialized chips. Monitoring the temperature of these hash boards is crucial. Most ASICs have built-in sensors reporting these temperatures. Optimal temperatures are typically in the 60-80°C range, with throttling or shutdown occurring above 90-95°C.
- Fan Health: ASIC fans are usually high-CFM, high-static pressure fans designed to push air directly through dense heatsinks. Their failure or degradation can quickly lead to overheating.
- Airflow Restriction: ASICs are extremely sensitive to airflow impedance. Any blockage at the intake or exhaust can cause significant temperature spikes.
ASIC Specific Thermal Strategies:
- Dedicated Airflow Pathways: Due to their concentrated heat output, ASICs demand dedicated, unimpeded airflow. In large farms, hot aisle/cold aisle containment is almost mandatory to ensure cool intake air and efficient exhaust of hot air. Each ASIC should have its own clear path for air intake and exhaust.
- Industrial-Grade Fan Systems: ASICs rely on powerful integrated fans. In cases where these are insufficient or fail, direct replacement with equally powerful or even more robust server-grade fans (e.g., Delta, NMB) is necessary. External booster fans or inline duct fans can also be used to assist airflow in challenging environments or over long duct runs.
- Strategic Exhaust Ventilation: The sheer volume of hot air exhausted by ASICs requires robust ventilation systems. This often involves large exhaust fans in the mining facility that can move tens of thousands of CFM, ensuring hot air is removed from the building and not recirculated. Ducting should be designed with minimal bends and optimal diameters to reduce static pressure.
- Immersion Cooling: For next-generation ASICs or very high-density deployments, immersion cooling is increasingly becoming the preferred solution. Submerging ASICs in dielectric fluid offers unparalleled cooling efficiency, noise reduction, and hardware longevity, transforming the thermal landscape of large-scale operations. It also opens up possibilities for waste heat recapture, turning a problem into a potential asset.
- Chip-Level Monitoring and Optimization: Advanced ASIC management software often allows for monitoring individual hash board temperatures. If one board consistently runs hotter, it might indicate a failing fan, dust buildup, or even a partially faulty chip. Some advanced firmware allows for individual chip frequency adjustment, enabling fine-tuning to reduce heat on specific problematic chips.
The distinct thermal signatures of GPUs and ASICs necessitate tailored approaches. While both benefit from cool ambient air and clear airflow, the level of direct user intervention and the types of cooling solutions employed differ substantially, reflecting their fundamental design and operational scales.
Energy Efficiency and Economic Considerations
Thermal management is not solely about protecting hardware; it’s intrinsically linked to the financial viability of a mining operation. Every watt consumed by cooling systems represents an operational cost, directly impacting profitability. Therefore, optimizing for energy efficiency in cooling is as crucial as optimizing mining hardware for hash rate per watt.
Power Usage Effectiveness (PUE)
The concept of Power Usage Effectiveness (PUE) is a standard metric borrowed from data center management that quantifies the energy efficiency of a facility. It is calculated as:
PUE = Total Facility Power / IT Equipment Power
Where:
- Total Facility Power: Includes all power consumed by the building, including IT equipment, cooling, lighting, and other infrastructure.
- IT Equipment Power: The power consumed solely by the mining hardware (ASICs, GPUs, CPUs).
A PUE of 1.0 would mean 100% of the energy consumed goes directly to the mining equipment, with no overhead for cooling, lighting, etc. In reality, a PUE of 1.0 is impossible. A PUE of 2.0 means that for every watt consumed by the mining hardware, another watt is consumed by supporting infrastructure, primarily cooling.
PUE Benchmarks:
- Typical Air-Cooled Residential/Small Scale: Often 1.5 – 2.0, sometimes higher if ventilation is poor.
- Well-Designed Air-Cooled Data Center/Farm: Aim for 1.2 – 1.5.
- Advanced Liquid Immersion Cooling: Can achieve PUEs as low as 1.05 – 1.15.
A lower PUE translates directly to lower operational expenditure (OpEx). For a large 10 MW mining farm, reducing PUE from 1.5 to 1.2 could save millions of dollars annually in electricity costs, making the initial investment in more efficient cooling infrastructure financially attractive over the long term. For example, if your mining hardware consumes 5 MW, and your PUE is 1.5, your total power consumption is 7.5 MW. If you can optimize your cooling to achieve a PUE of 1.2, your total power consumption drops to 6 MW, saving 1.5 MW, which at a cost of $0.05/kWh equates to $657,000 in annual savings.
Cost-Benefit Analysis of Cooling Investments
Investing in advanced cooling solutions, whether it’s high-quality fans, custom liquid loops, or full immersion systems, comes with an upfront capital expenditure (CapEx). This investment must be weighed against the potential OpEx savings and the tangible benefits of increased hardware longevity and performance.
Cooling Method | Initial CapEx (Relative) | OpEx (Cooling Energy, Relative) | Hardware Longevity Benefit | Performance Gain |
---|---|---|---|---|
Basic Air Cooling (Fans) | Low | Moderate-High | Minimal (depends on ambient) | Limited |
Optimized Air Cooling (Hot/Cold Aisles, Filters) | Medium | Moderate | Moderate | Modest |
AIO/Custom Liquid (GPUs) | Medium-High | Low-Moderate | Significant | High (stable OC) |
Single-Phase Immersion | High | Low | Very Significant | Very High (stable OC) |
Two-Phase Immersion | Very High | Very Low | Exceptional | Extreme |
The “breakeven point” for a more expensive cooling solution occurs when the accumulated OpEx savings (from lower cooling power consumption and fewer hardware replacements due to thermal stress) offset the initial CapEx. For a long-term mining operation, investing in superior thermal management almost always yields a positive return on investment.
Waste Heat Recovery and Reuse
A significant and often overlooked aspect of economic efficiency is the potential for waste heat recovery. Mining hardware, by its nature, converts electrical energy into useful computation and heat. This heat, traditionally considered a waste product, can be a valuable resource.
- Space Heating: The simplest form of heat recovery involves using the warm exhaust air from mining rigs to heat adjacent living or working spaces, greenhouses, or even swimming pools. This can significantly reduce heating bills in colder climates. Some commercial products are specifically designed as “mining heaters.”
- Water Heating: For liquid immersion systems, the heated dielectric fluid can be passed through a heat exchanger to warm water for domestic or industrial use. This concept is being explored for district heating systems in some municipalities.
- Agricultural Applications: The warm air or water can be used to create controlled environments for aquaculture (fish farming) or hydroponic farming, extending growing seasons or enabling cultivation of specific crops in otherwise unsuitable climates.
While waste heat recovery adds complexity to the initial setup, it transforms a cost center (heat rejection) into a potential revenue stream or significant cost saving, further improving the overall economic efficiency and sustainability of a mining operation. As energy prices fluctuate and environmental concerns grow, the ability to repurpose waste heat becomes an increasingly important differentiator for large-scale mining operations. This strategic approach moves beyond mere thermal management to holistic energy management, driving down the true cost of digital asset production.
Site Selection and Infrastructure Considerations for Optimal Thermal Performance
The physical environment and supporting infrastructure of a mining operation are as critical to thermal management as the cooling hardware itself. Overlooking these foundational elements can severely limit the effectiveness of even the most sophisticated cooling systems.
Climate and Geographic Location
The ambient climate of your chosen mining location fundamentally dictates the cooling challenges you will face.
- Cold Climates: Locations with consistently low ambient temperatures (e.g., Nordic countries, Northern Canada, Siberia) offer a natural advantage for air-cooled mining. Free-cooling (using outdoor air for cooling without mechanical refrigeration) is highly efficient, often requiring only robust ventilation. This dramatically reduces cooling OpEx. However, considerations must be given to humidity control in very cold, dry air to prevent static electricity, and ensuring components don’t become excessively cold during shutdowns.
- Temperate Climates: These regions experience seasonal variations. Cooling systems must be designed to handle warm summer peaks, often requiring a combination of free-cooling for colder months and mechanical cooling (e.g., chillers, swamp coolers) for warmer periods.
- Hot Climates: Tropical or desert regions present the most significant thermal challenges. High ambient temperatures necessitate powerful mechanical cooling systems, potentially leading to higher OpEx. Immersion cooling or highly efficient evaporative cooling (where applicable) may become more economically viable. Dust and sand are also major concerns in desert environments, requiring advanced filtration.
Choosing a location with a favorable climate can significantly reduce the complexity and cost of cooling infrastructure, directly impacting the long-term profitability of the mining venture.
Building Design and Insulation
The physical structure housing your mining operation plays a crucial role in maintaining stable internal temperatures.
- Insulation: Proper insulation in walls, roofs, and floors helps to prevent external heat from entering the facility in hot climates and to retain heat in cold climates if waste heat recovery is being utilized. This reduces the load on cooling or heating systems.
- Roofing Material: Light-colored or reflective roofing materials can significantly reduce solar heat gain compared to dark materials, lowering the internal ambient temperature.
- Window Management: Minimize windows, especially those facing direct sunlight, or use high-performance, low-emissivity glass to reduce heat transfer.
- Dedicated Airflow Paths: The building design should naturally facilitate the movement of air, allowing for clear intake and exhaust pathways. High ceilings can help hot air rise, making it easier to exhaust. Designing for hot aisle/cold aisle containment from the ground up simplifies implementation and maximizes efficiency.
- Thermal Mass: Materials with high thermal mass (e.g., concrete walls) can absorb and release heat slowly, helping to stabilize internal temperatures and buffer against rapid external temperature swings.
Power Infrastructure for Cooling Systems
Cooling systems, especially mechanical refrigeration units or large fan arrays, can consume a substantial amount of electricity. The electrical infrastructure must be robust enough to support not only the mining hardware but also the cooling apparatus.
- Adequate Capacity: Ensure the incoming electrical service, transformers, switchgear, and distribution panels have sufficient capacity to handle the combined load of mining equipment and cooling systems, with a comfortable buffer for future expansion or peak demand.
- Redundancy: For critical operations, redundant power feeds or backup generators for cooling systems are essential to prevent catastrophic overheating during power outages.
- Voltage Considerations: Running large cooling equipment on higher voltages (e.g., 480V three-phase) can be more efficient and reduce current draw compared to lower voltages, minimizing losses and enabling smaller gauge wiring.
- Circuit Segregation: Ideally, power for cooling systems should be on separate circuits from the mining equipment itself, allowing for easier maintenance, troubleshooting, and load balancing.
Water Availability and Quality (for Liquid Cooling)
For operations relying on water-cooled systems (e.g., chillers, liquid-to-liquid heat exchangers, or even evaporative cooling towers), access to a reliable supply of water of suitable quality is paramount.
- Supply Volume: Ensure sufficient water flow and pressure for the cooling system’s needs.
- Water Quality: High mineral content (hard water) can lead to scaling and corrosion in cooling pipes and heat exchangers. Filtration and water treatment systems (e.g., deionization, reverse osmosis) may be necessary to prevent these issues, adding to OpEx.
- Disposal/Recirculation: Consider regulations for wastewater discharge or implement closed-loop systems to minimize water consumption and environmental impact.
Noise Abatement
High-performance cooling fans, especially those used in ASICs or large server rooms, generate significant noise. This is a critical consideration for residential operations or farms located near populated areas.
- Acoustic Treatment: Insulating walls, installing sound-dampening panels, or using specialized acoustic baffling in air ducts can mitigate noise pollution.
- Fan Selection: Opt for larger, slower-spinning fans that move more air at lower RPMs, reducing noise levels. For ASICs, external silencers can be fitted to exhaust ducts.
- Immersion Cooling: This method inherently eliminates the need for ASIC/GPU fans, drastically reducing noise levels within the mining facility.
A holistic approach to site selection and infrastructure development, incorporating these thermal considerations from the outset, lays the groundwork for a robust, efficient, and economically sustainable mining operation, minimizing future complications and maximizing long-term profitability.
Advanced Cooling Techniques and Future Trends
The relentless pursuit of higher hash rates and greater energy efficiency in cryptocurrency mining continues to drive innovation in thermal management. Beyond conventional air and liquid cooling, several advanced techniques are emerging, and future trends promise even greater leaps in thermal control.
Refrigeration-Assisted Cooling (Chillers)
While less common for individual rigs due to complexity and cost, chillers are industrial-scale refrigeration units that actively cool a liquid coolant (typically water or a glycol mixture) to below ambient temperatures. This chilled liquid is then circulated through heat exchangers (or directly into water blocks) to cool mining hardware.
Pros:
- Extreme Cooling Performance: Can bring temperatures down to levels unachievable with passive or evaporative methods, even in very hot climates.
- Precise Temperature Control: Offers very tight control over coolant temperature, ensuring stable operating conditions.
- High Heat Dissipation: Capable of handling massive thermal loads.
Cons:
- High Energy Consumption: Mechanical refrigeration is energy-intensive, significantly increasing OpEx. This is reflected in a higher PUE unless waste heat is effectively recaptured.
- High Initial CapEx: Chillers and associated plumbing are very expensive.
- Complexity & Maintenance: Requires specialized knowledge for installation and ongoing maintenance.
Chillers are generally reserved for very high-density operations in warm climates where free-cooling is not an option, and the value of sustained uptime and performance outweighs the increased energy cost.
Two-Phase Immersion Cooling with Ultra-Low Boiling Point Fluids
As discussed previously, two-phase immersion cooling is an advanced form of liquid cooling. The future of this technology lies in the development of even more efficient and cost-effective dielectric fluids, alongside optimized tank designs that maximize heat exchange. Research is ongoing into novel fluids with even lower boiling points and better thermodynamic properties, potentially pushing hardware to even cooler operating temperatures or allowing for greater densities. The integration of advanced condensation systems, perhaps leveraging external cooling loops with very low temperatures, will further enhance their efficiency.
Vapor Chambers and Advanced Heat Pipes
Modern high-performance GPUs and ASICs already incorporate sophisticated heat pipe technology and, increasingly, vapor chambers into their heatsink designs. These components are extremely efficient at transferring heat from a concentrated source to a larger dissipation area.
- Heat Pipes: Utilize a wick structure and a working fluid (e.g., water, ammonia) sealed under vacuum. Heat applied at one end vaporizes the fluid, which then travels to the cooler end, condenses, and returns via the wick.
- Vapor Chambers: Essentially a flattened heat pipe, a vapor chamber provides a larger, more uniform heat spreading surface. This allows for highly efficient heat transfer from a large, concentrated heat source (like a GPU die) to an attached fin stack.
Future trends include more sophisticated geometries, novel working fluids, and integration of these technologies directly into silicon packages or substrates, allowing for more efficient heat removal directly at the chip level, reducing the reliance on bulky external heatsinks.
AI-Driven Thermal Management Systems
The advent of artificial intelligence and machine learning is poised to revolutionize thermal management in large-scale mining operations. Instead of static fan curves or fixed temperature thresholds, AI-driven systems can:
- Predictive Analysis: Analyze historical temperature data, power consumption, ambient conditions, and even weather forecasts to predict thermal trends and proactively adjust cooling parameters before temperatures become critical.
- Dynamic Optimization: Continuously learn and adapt cooling strategies in real-time. For example, dynamically adjusting fan speeds, chiller output, or even individual miner power limits based on current and predicted thermal loads, energy prices, and hash rate targets.
- Anomaly Detection: Identify subtle deviations in temperature or fan speed patterns that might indicate an impending hardware failure, allowing for preventative maintenance.
- Energy Efficiency Optimization: Find the optimal balance between cooling performance and energy consumption, minimizing PUE by making intelligent decisions about when to use active vs. passive cooling, or how aggressively to run fans.
These systems could potentially reduce cooling energy consumption by an additional 10-20% beyond what traditional static controls achieve, while simultaneously enhancing hardware reliability.
Sustainable Cooling Practices and Waste Heat Valorization
Beyond merely managing heat, the future of mining thermal management increasingly focuses on sustainability. This involves:
- Renewable Energy Integration: Powering cooling systems with renewable energy sources (solar, wind, hydroelectric) to reduce carbon footprint.
- Advanced Waste Heat Recovery: Expanding on current waste heat reuse applications to integrated energy solutions, where mining facilities become co-generation plants providing heat for district heating, industrial processes, or highly efficient greenhouses.
- Modular and Portable Solutions: Developing cooling systems that are highly efficient, scalable, and adaptable to various climates and temporary deployments, potentially allowing mining to leverage intermittent or stranded renewable energy sources.
The trajectory of thermal management in cryptocurrency mining is towards increasingly sophisticated, efficient, and sustainable solutions. As hardware becomes more powerful and heat-dense, the innovations in cooling will be crucial not only for pushing performance boundaries but also for ensuring the economic viability and environmental responsibility of the entire industry.
Maintaining optimal temperatures for your mining hardware is not a trivial task; it is a complex, multifaceted discipline that directly impacts the performance, longevity, and profitability of your operations. From the foundational principles of heat transfer to the intricacies of environmental factors, and from the ubiquitous air-cooled setups to the cutting-edge of two-phase immersion, every decision in thermal management carries significant weight. We’ve explored how understanding fan metrics, airflow dynamics, and hot/cold aisle containment can optimize traditional air cooling, while liquid solutions like AIOs, custom loops, and full immersion offer escalating levels of thermal control for increasingly dense and powerful hardware. The role of continuous monitoring, intelligent software, and diligent preventative maintenance — including regular cleaning and critical thermal interface material replacements — cannot be overstated, acting as the vigilant guardians of your valuable assets. Furthermore, tailoring cooling strategies to the specific demands of GPUs versus ASICs ensures targeted efficiency. Crucially, the economic implications, measured by metrics like PUE and the potential for waste heat recovery, transform thermal management from a mere operational cost into a strategic investment. As the industry evolves, embracing advanced techniques like refrigeration-assisted cooling, AI-driven optimization, and sustainable practices will be paramount for securing a competitive edge and ensuring the long-term viability of digital asset generation. Ultimately, mastering temperature control isn’t just about keeping things cool; it’s about maximizing return on investment, minimizing environmental impact, and future-proofing your mining endeavors.
Frequently Asked Questions (FAQ)
Q1: How hot is too hot for a GPU or ASIC miner?
A1: For most GPU cores, sustained temperatures above 80-85°C are considered high and can lead to throttling and accelerated degradation. For GDDR6X VRAM, junction temperatures consistently above 95-100°C are critical and should be addressed immediately. ASIC hash boards typically perform optimally between 60-80°C, with throttling often occurring around 90-95°C. Always consult your specific hardware manufacturer’s recommended operating temperatures.
Q2: Can I use household fans or air conditioners to cool my mining rigs?
A2: While household fans can provide some airflow, they typically lack the static pressure and CFM to effectively cool high-density mining hardware. They are generally insufficient for anything more than a single, low-power rig. Household air conditioners can reduce ambient room temperature, which helps, but they are not designed for direct, concentrated heat removal from individual components and are often energy-inefficient for this purpose compared to dedicated cooling solutions like hot/cold aisle containment or immersion systems.
Q3: How often should I replace the thermal paste and pads on my mining GPUs?
A3: For mining GPUs, especially those with GDDR6X memory, it’s generally recommended to replace thermal paste and pads every 12-18 months. The continuous high temperatures and operational stresses in a mining environment can degrade these materials faster than in typical gaming PCs. If you observe consistently high VRAM junction temperatures (e.g., above 95°C) even with good airflow, an earlier replacement might be necessary.
Q4: What is the most energy-efficient cooling method for large-scale mining operations?
A4: For large-scale operations, the most energy-efficient cooling method often depends on the local climate. In cold climates, optimized air cooling with free-cooling (using outdoor air) is highly efficient. However, for high-density setups or in warmer climates, single-phase immersion cooling typically offers the lowest Power Usage Effectiveness (PUE) and best overall energy efficiency due to its superior heat transfer capabilities and potential for waste heat recovery. Two-phase immersion offers even greater efficiency but with significantly higher initial costs.
Q5: Is dust a major concern for liquid-cooled mining systems?
A5: For custom liquid loops, dust is less of a concern for the submerged components but can still accumulate on radiators, reducing their air-cooling efficiency. Regular cleaning of radiators is still necessary. For full immersion cooling, the hardware is completely submerged in a sealed environment, making dust a non-issue for the submerged components themselves. This is a significant advantage over air-cooled systems regarding dust management and hardware protection.
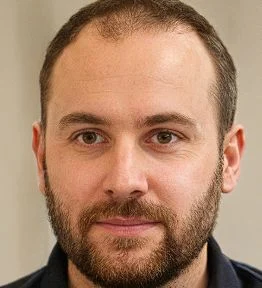
Michael combines data-driven research with real-time market insights to deliver concise crypto and bitcoin analysis. He’s passionate about uncovering on-chain trends and helping readers make informed decisions.